Sheet Metal Fabrication: An Essential Process in Manufacturing
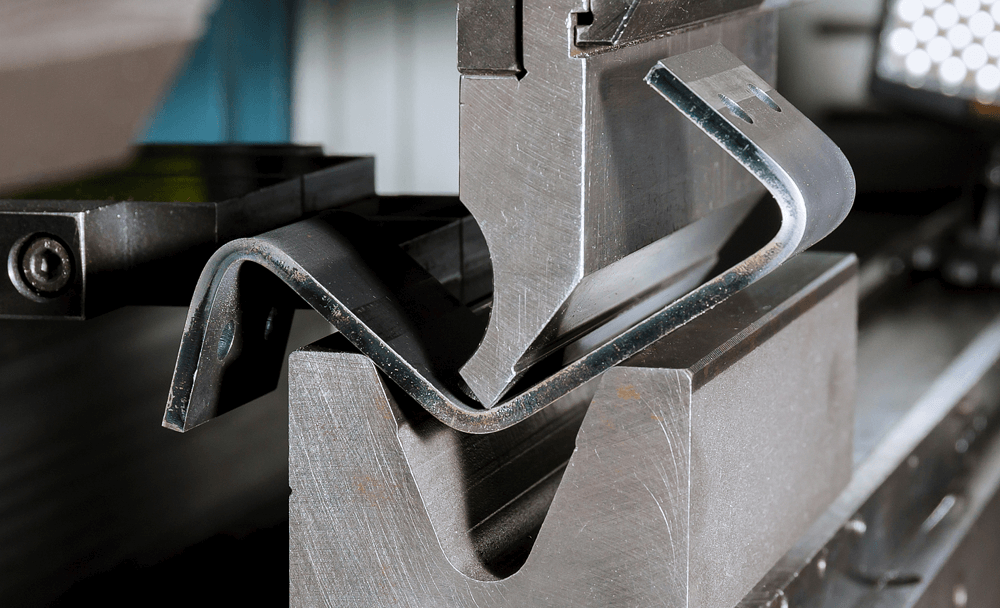
Sheet metal fabrication is a critical process in manufacturing that involves the manipulation and transformation of flat sheets of metal into various products. It is widely used across numerous industries, including automotive, aerospace, electronics, construction, and HVAC (heating, ventilation, and air conditioning). This versatile process can create everything from structural components to intricate designs and products. Understanding the fundamentals of sheet metal fabrication, the techniques used, and its applications can provide valuable insights into the importance of this process in modern manufacturing.
What is Sheet Metal Fabrication?
Sheet metal fabrication refers to the process of transforming flat sheets of metal into specific shapes, sizes, and structures through various techniques. These techniques include cutting, bending, welding, punching, stamping, and assembling metal sheets to create functional or decorative components. The metal used in sheet metal fabrication can include steel, aluminum, brass, copper, or even specialty metals like titanium.
The process generally begins with a flat, thin sheet of metal. The sheet is then worked on using machines or manual labor to perform tasks like shaping, bending, and cutting to create the desired part or product. Depending on the complexity of the design, the process can be simple or highly sophisticated.
The Key Techniques in Sheet Metal Fabrication
Sheet metal fabrication involves several core techniques that work together to achieve the desired end product. These techniques can be broken down into the following categories:
1. Cutting
Cutting is one of the most fundamental processes in sheet metal fabrication. It involves removing parts of the sheet to create the desired shape. There are several methods of cutting, including:
- Laser Cutting: Laser cutting uses a high-powered laser beam to cut through metal sheets with extreme precision. This technique is ideal for intricate designs and precise cuts in a wide variety of metals.
- Water Jet Cutting: This method uses a high-pressure jet of water mixed with abrasive materials to cut through metal. It is particularly useful for cutting thick metals and when heat-sensitive materials are involved.
- Shearing: Shearing involves using a pair of blades to cut metal sheets. It is often used for straight-line cuts and is commonly found in industrial settings.
- Plasma Cutting: Plasma cutting uses a jet of hot plasma to melt and cut through metal sheets. It is suitable for cutting thicker materials and is more cost-effective than laser cutting for certain applications.
2. Bending
Bending is a process that involves deforming the sheet metal to form angles, curves, or complex shapes. The metal is typically bent using a press brake, which applies force to the sheet to create the desired bend. This process is essential when the final product needs to have specific angles or contours, such as in the automotive industry for creating parts like chassis or brackets.
Bending can be performed using different techniques, including:
- Air Bending: In this technique, the sheet metal is bent without the metal fully coming in contact with the die.
- Bottoming: In bottoming, the metal is bent fully using the die.
- Coining: Coining is a precise bending technique that applies force to the sheet metal to create fine, detailed bends.
3. Welding
Welding is a crucial step in sheet metal fabrication that involves joining two or more pieces of metal together. This is achieved by melting the edges of the metal sheets and allowing them to fuse. There are various types of welding techniques used in sheet metal fabrication, including:
- TIG Welding (Tungsten Inert Gas): Known for producing clean, high-quality welds, TIG welding is often used when welding thin metal sheets, particularly stainless steel or aluminum.
- MIG Welding (Metal Inert Gas): MIG welding is a faster, more efficient method commonly used for larger projects where speed is important. It uses a continuous wire feed to create a weld between two metal sheets.
- Spot Welding: This is a method of joining sheet metals at specific points through the use of electrodes. Spot welding is often used in automotive manufacturing to attach panels and other parts.
4. Punching and Stamping
Punching and stamping involve creating holes or shapes in metal sheets by pressing them between dies. This technique is particularly useful for producing high volumes of parts quickly and efficiently. The primary difference between punching and stamping is that punching is generally used for creating holes, while stamping can create more intricate shapes or patterns.
- Punching: In this method, a punch tool is used to create holes in the metal sheet. This is commonly used for applications such as creating ventilation holes or mounting points in metal products.
- Stamping: Stamping is a more complex process that involves pressing the metal sheet into a die to create parts with a three-dimensional shape. It is commonly used in the automotive industry for parts like body panels.
5. Finishing
Once the sheet metal has been cut, bent, and welded into shape, it often requires finishing processes to achieve the desired surface texture or to protect the metal. Common finishing techniques include:
- Powder Coating: Powder coating is a type of dry finishing process that involves applying a fine powder to the metal surface before baking it at high temperatures to create a smooth, durable coating.
- Painting: Traditional painting techniques are also used to apply protective or decorative coatings to sheet metal products.
- Anodizing: This process is used for aluminum, in which the metal is treated to form a protective oxide layer on its surface. Anodizing improves corrosion resistance and provides a decorative finish.
Applications of Sheet Metal Fabrication
Sheet metal fabrication is a versatile process that can be applied to a wide range of industries. Some of the most common applications include:
1. Automotive Industry
In the automotive industry, sheet metal fabrication is used to create various components, such as car body panels, chassis, engine parts, and brackets. The process helps achieve both structural integrity and aesthetic appeal.
2. Aerospace Industry
In aerospace, precision is paramount. Sheet metal fabrication is used to produce parts for aircraft, including wings, fuselages, and landing gear. These parts require high-strength materials and precision manufacturing techniques, making sheet metal fabrication indispensable.
3. Construction and Architecture
Sheet metal fabrication plays a significant role in the construction industry for creating structural components like beams, frames, and roofing systems. Additionally, it is used for architectural features such as decorative facades, cladding, and custom-made elements.
4. HVAC Systems
Heating, ventilation, and air conditioning (HVAC) systems rely on sheet metal fabrication to create ductwork, vents, and other components. The durability and flexibility of sheet metal make it an ideal material for building HVAC systems that need to withstand extreme temperatures and environmental conditions.
5. Electronics and Consumer Goods
In the electronics and consumer goods industries, sheet metal fabrication is used to create enclosures, housings, and other structural components for devices such as computers, telecommunication equipment, and kitchen appliances.
The Future of Sheet Metal Fabrication
As technology continues to advance, the future of sheet metal fabrication is looking brighter than ever. Innovations like automation, robotic welding, and 3D printing are making the fabrication process faster, more precise, and more cost-effective. With these advancements, manufacturers are able to create more complex designs, reduce waste, and increase production efficiency.
Additionally, the growing trend of sustainability in manufacturing means that the recycling and reuse of metals used in sheet metal fabrication are becoming increasingly important. With improved environmental regulations and practices, sheet metal fabrication is evolving to be both economically and ecologically sustainable.
Conclusion
Sheet metal fabrication is a cornerstone of modern manufacturing that enables the creation of countless products used in everyday life. By employing a wide array of techniques like cutting, bending, welding, and finishing, manufacturers can produce everything from industrial components to decorative designs. As industries continue to demand higher quality, greater precision, and faster production speeds, sheet metal fabrication will remain a vital process in shaping the future of manufacturing.