Why HDPE Pipes Are Essential in Mining and Industrial Operations
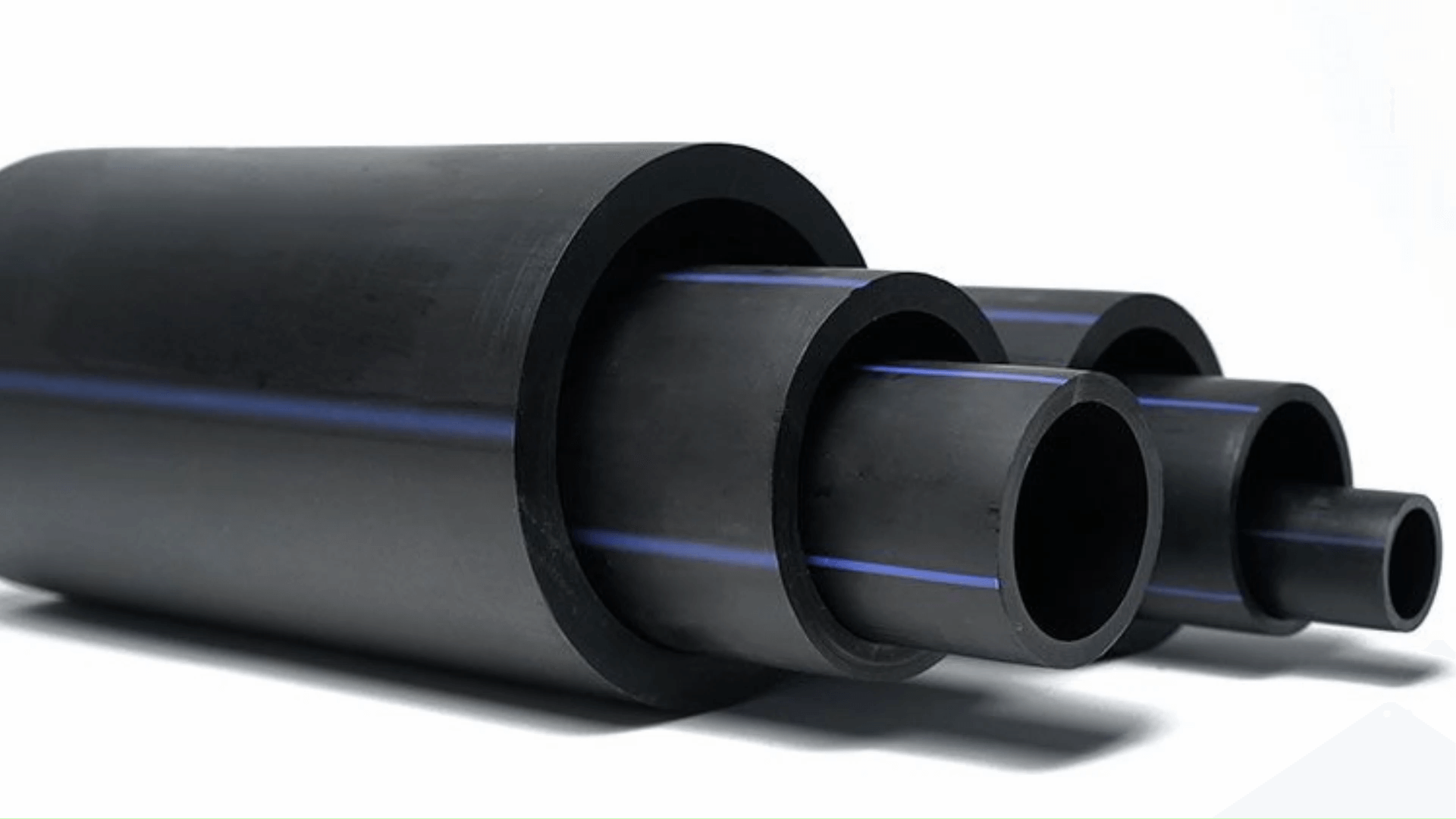
Introduction
In mining and industrial operations, infrastructure demands materials that withstand extreme conditions and deliver durability, safety, and efficiency. One material that meets these requirements exceptionally well is HDPE (High-Density Polyethylene) pipes. Known for their strength, flexibility, and resistance to chemicals, HDPE pipes have become indispensable in these sectors. This article dives into why HDPE pipes are increasingly chosen in mining and industrial applications, particularly in regions like Pakistan, where environmental and operational challenges demand robust solutions.
What Are HDPE Pipes?
HDPE pipes are made from high-density polyethylene, a plastic material valued for its resilience. Compared to traditional materials like steel or PVC, HDPE pipes offer unique advantages such as flexibility, resistance to corrosion, and ease of installation.
Key Characteristics of HDPE Pipes:
- High Strength-to-Density Ratio: Durable yet lightweight, making them easy to transport and install.
- Chemical Resistance: Withstands exposure to aggressive chemicals and acids.
- UV Resistance: Designed to resist ultraviolet degradation, they are suitable for outdoor applications.
- Environmental Friendliness: Fully recyclable, helping reduce the carbon footprint of mining and industrial projects.
Key Properties of HDPE Pipes in Mining and Industrial Applications
Mining and industrial environments present harsh conditions that most materials can’t endure long-term. Here’s why HDPE pipes are ideally suited for these demanding sectors:
-
Durability and Longevity
- Resistant to abrasion, corrosion, and UV degradation, HDPE pipes can last for decades without significant deterioration.
- These pipes are also resilient to mechanical damage, which reduces the need for frequent repairs.
-
Flexibility
- HDPE pipes can bend without breaking, which is beneficial for installation across rugged terrains or in confined spaces.
- They are also ideal for underground and underwater applications, where movement or shifting soil could damage rigid pipes.
-
Chemical and Thermal Resistance
- HDPE pipes can handle extreme temperatures and a variety of aggressive chemicals without losing integrity.
- This resistance is precious in mining, where pipes frequently transport corrosive materials.
-
Environmental Impact
- HDPE pipes are made from recyclable materials and support sustainable development goals by reducing waste.
- Unlike steel, HDPE does not rust, which means fewer contaminants are introduced into the surrounding soil or water.
Applications of HDPE Pipes in Mining
In the mining sector, HDPE pipes are used extensively for their adaptability and strength in handling everything from water management to the transport of highly abrasive materials.
-
Water Management
- HDPE pipes help manage water flow for dust suppression, cooling, and even drinking water supply for miners.
- Their leak-resistant joints minimize the risk of contamination in water sources, a crucial aspect of environmentally responsible mining.
-
Slurry Transport
- Slurries containing crushed rock and other materials are highly abrasive, but HDPE’s resilience allows it to handle such materials with minimal wear.
- HDPE pipes extend the life of slurry systems, reducing downtime and maintenance costs.
-
Chemical Transport
- In mining, various chemicals are used in extraction and refining. HDPE pipes are safe for transporting acidic, alkaline, or otherwise reactive chemicals.
- This property reduces the risk of pipe failure, improving both operational safety and cost efficiency.
-
Ventilation and Drainage Systems
- In underground mines, HDPE pipes support ventilation systems and drainage channels to manage air quality and water buildup.
- HDPE’s lightweight nature simplifies installation in hard-to-reach areas, ensuring mines remain safe and compliant with safety standards.
Industrial Uses of HDPE Pipes
Beyond mining, HDPE pipes play a significant role in various industrial applications, offering versatile solutions for sectors ranging from agriculture to construction.
-
Oil and Gas Pipelines
- HDPE pipes are a preferred material for transporting oil, gas, and other fuels due to their resistance to chemicals and high pressure tolerance.
- They also offer a lower maintenance solution, with a reduced risk of leaks that could lead to environmental damage.
-
Agriculture and Irrigation
- HDPE pipes are widely used in large-scale agriculture for efficient water distribution. Their durability and low maintenance needs make them a cost-effective solution.
- Farmers use these pipes for irrigation channels that can withstand exposure to fertilizers and pesticides without corrosion.
-
Construction and Infrastructure
- HDPE pipes are employed in the construction of drainage and stormwater management systems. Their flexibility allows installation in various terrains and climates.
- The smooth inner surface reduces friction, increasing water flow efficiency and minimizing blockages.
-
Manufacturing Plants
- Many factories use HDPE pipes for cooling and waste management systems. The pipes’ chemical resistance is valuable in managing industrial waste safely.
- HDPE’s longevity means fewer disruptions in plants where constant operational flow is essential.
Benefits of HDPE Pipes Over Traditional Metal Pipes in Mining and Industry
Choosing HDPE pipes over traditional options like metal pipes brings significant advantages in the long run:
-
Corrosion Resistance
- Unlike metal pipes, HDPE pipes are immune to rust, meaning they maintain structural integrity even after prolonged exposure to moisture.
- This quality is crucial in sectors where exposure to corrosive materials is a daily occurrence.
-
Lightweight and Easy Installation
- HDPE pipes are significantly lighter than metal, making transport and installation simpler and cheaper.
- This reduced weight also lowers labor requirements, helping companies save on operational costs.
-
Reduced Leakage
- HDPE pipes utilize fusion welding, resulting in virtually leak-proof joints that prevent costly material losses.
- This feature is particularly valuable in high-stakes environments like mining, where leaks can disrupt production and pose environmental risks.
-
Flexibility in Design and Installation
- HDPE pipes’ flexibility allows custom solutions to meet the unique layout and requirements of complex sites, including twisting routes or steep inclines.
- With fewer breakpoints, HDPE pipes provide reliable performance even in challenging conditions.
Safety and Compliance Standards for HDPE Pipes in Mining and Industry
Safety and compliance are essential in mining and industrial applications. HDPE pipes meet various international standards that ensure their safety, quality, and durability in high-stress environments.
-
International Standards Compliance
- HDPE pipes adhere to ISO, ASTM, and AWWA standards, ensuring they meet or exceed safety requirements.
- Compliance with these standards provides peace of mind to industries relying on high-quality materials.
-
Environmental Compliance
- HDPE pipes support environmental goals as they are fully recyclable and resistant to rust and corrosion, reducing environmental contaminants.
- Their durability means fewer replacements, minimizing waste generation over time.
-
Selection of Certified Manufacturers
- It’s essential to source HDPE pipes from certified manufacturers to ensure adherence to industry standards.
- Certified pipes are often tested for resistance to UV light, temperature extremes, and chemical exposure, ensuring quality and reliability.
Challenges and Considerations in Using HDPE Pipes in Mining and Industry
While HDPE pipes offer many advantages, some challenges should be considered to maximize their performance in industrial settings.
-
UV Exposure
- Long-term UV exposure can degrade HDPE pipes. Applying UV-resistant coatings or using black-colored HDPE (inherently UV-resistant) can mitigate this issue.
-
Temperature Sensitivity
- HDPE pipes are sensitive to high temperatures and may become more flexible in extreme heat. Proper installation practices can minimize any negative impact.
-
Joining Techniques
- Proper fusion welding is essential to ensure strong, leak-proof joints. This requires skilled technicians and quality equipment, as poorly joined pipes may compromise system integrity.
Tips for Smooth Installation and Usage:
- Use certified installers familiar with HDPE’s specific requirements.
- Consider environmental conditions, including temperature and UV exposure, before installation.
- Regularly inspect pipes for signs of degradation or wear in exposed applications.
Case Studies and Success Stories
Case Study #1: Mining Project in Australia
A mining project in Australia faced challenges with traditional steel pipes, which corroded rapidly in acidic environments. Switching to HDPE pipes increased the system’s lifespan by over 20 years, reduced maintenance costs by 60%, and minimized environmental contamination risks.
Case Study #2: Industrial Facility in Pakistan
An industrial plant in Pakistan implemented HDPE pipes in their cooling systems, achieving improved operational efficiency and reduced maintenance costs. HDPE’s chemical resistance allowed the plant to avoid costly shutdowns for pipe repairs, saving substantial time and resources.
Conclusion
HDPE pipes have proven to be essential assets in the mining and industrial sectors, thanks to their durability, flexibility, and cost-effectiveness. As industries worldwide, including those in Pakistan, face increased demands for resilient, environmentally responsible solutions, HDPE pipes offer a sustainable alternative that meets rigorous performance standards.
For any mining or industrial operation, switching to HDPE pipes represents not only a technical upgrade but also a step toward a more sustainable, reliable infrastructure. When durability, environmental impact, and cost savings are paramount, HDPE pipes deliver unparalleled value.