3D Printing vs Vacuum Casting: A Complete Guide for Manufacturers 2024
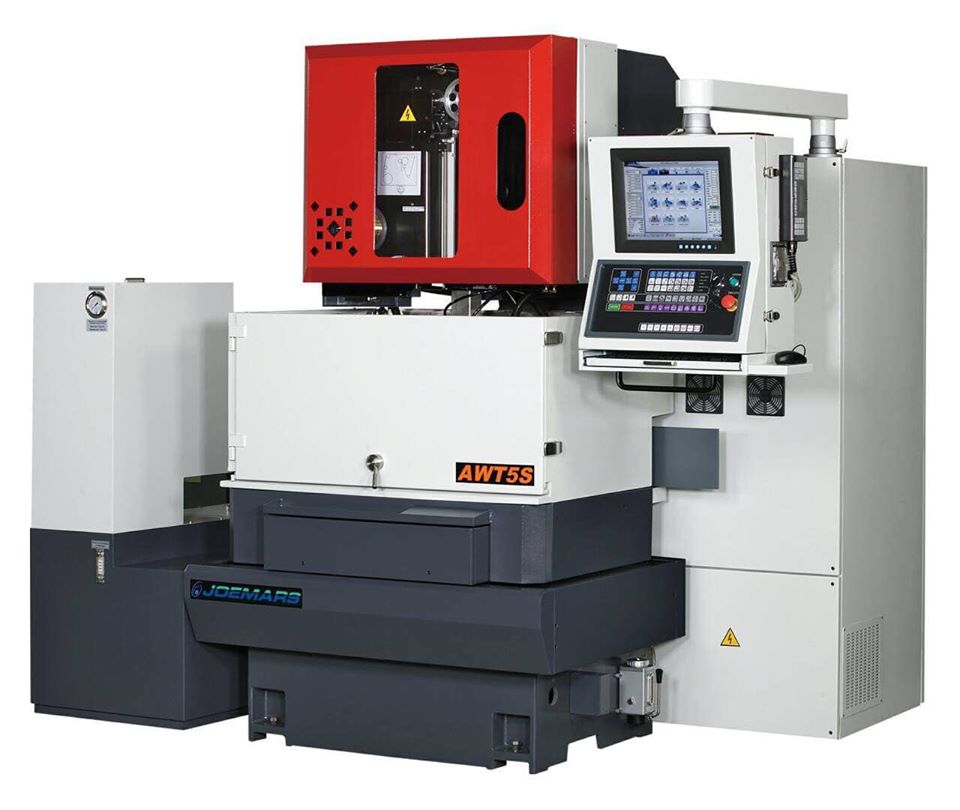
The Ultimate Guide to Modern Prototyping: Understanding 3D Printing and Vacuum Casting
In today’s rapidly evolving manufacturing landscape, choosing the right production method can make or break your project’s success. As a manufacturing consultant with two decades of experience, I’ve witnessed firsthand how advanced additive manufacturing techniques like 3D printing and professional vacuum casting services have revolutionized the prototyping industry.
Key Differences Between Technologies
Feature | 3D Printing | Vacuum Casting |
---|---|---|
Initial Cost | Lower | Moderate |
Production Speed | 24-48 hours | 3-5 days |
Surface Finish | Layer lines visible | Smooth, injection-molded like |
Material Options | Limited | Extensive |
Production Volume | 1-10 pieces | 10-50 pieces |
Accuracy | ±0.1mm | ±0.05mm |
Understanding 3D Printing Technology
Modern 3D printing has evolved significantly from its early days. This technology builds objects layer by layer, offering unprecedented design freedom. Here are the main advantages:
- Rapid prototyping capability with minimal setup
- Complex geometries without additional cost
- No tooling required
- Customization at scale
- Immediate design iterations
- Reduced material waste
Materials and Applications
The range of materials available for 3D printing continues to expand:
- Engineering plastics (ABS, PLA, PETG)
- High-performance polymers (PEEK, ULTEM)
- Flexible materials (TPU, TPE)
- Metal-infused filaments
- Ceramic composites
Vacuum Casting: The Bridge to Production
Vacuum casting represents a crucial stepping stone between prototyping and mass production. This technology creates high-quality parts that closely mirror injection-molded components. When considering vacuum casting services, understanding its benefits is essential:
Process Benefits
- Superior surface finish
- Excellent dimensional accuracy
- Cost-effective for medium runs
- Wide material selection
- Faster than traditional tooling
- Perfect for functional prototypes
Choosing Between Technologies
Several factors influence the choice between 3D printing and vacuum casting:
Budget Considerations:
- Equipment investment
- Material costs
- Labor requirements
- Production volume
- Post-processing needs
Time Constraints:
- Design validation speed
- Production turnaround
- Market testing requirements
- Development timeline
Advanced Applications and Industry Trends
The manufacturing landscape continues to evolve, with both 3D printing technology and vacuum casting finding new applications:
Healthcare:
- Custom medical devices
- Anatomical models
- Surgical guides
- Dental applications
Automotive:
- Functional prototypes
- Custom parts
- Testing components
- Interior elements
Material Selection Guidelines
3D Printing Materials
- Consider end-use requirements
- Evaluate mechanical properties
- Check temperature resistance
- Assess chemical compatibility
- Review surface finish needs
Vacuum Casting Materials
- Polyurethane options
- Silicone varieties
- Rubber-like materials
- Transparent resins
- High-impact compounds
Cost Analysis and ROI
Understanding the financial implications of each technology is crucial:
Investment Factors:
- Initial equipment costs
- Material expenses
- Training requirements
- Maintenance needs
- Production volumes
Quality Control and Validation
Both technologies require specific quality control measures:
3D Printing Checks:
- Layer adhesion
- Dimensional accuracy
- Surface finish
- Internal structure
- Material consistency
Vacuum Casting Verification:
- Mold quality
- Air entrapment
- Curing parameters
- Surface defects
- Part consistency
Future Trends and Developments
The landscape of both 3D printing and vacuum casting continues to evolve with emerging technologies and applications. Industry experts predict several developments:
Emerging Trends:
- AI-driven design optimization
- Hybrid manufacturing systems
- Advanced material development
- Automated quality control
- Sustainable production methods
Making the Final Decision
Consider these key points when choosing between technologies:
- Production volume requirements
- Surface finish expectations
- Material property needs
- Budget constraints
- Timeline requirements